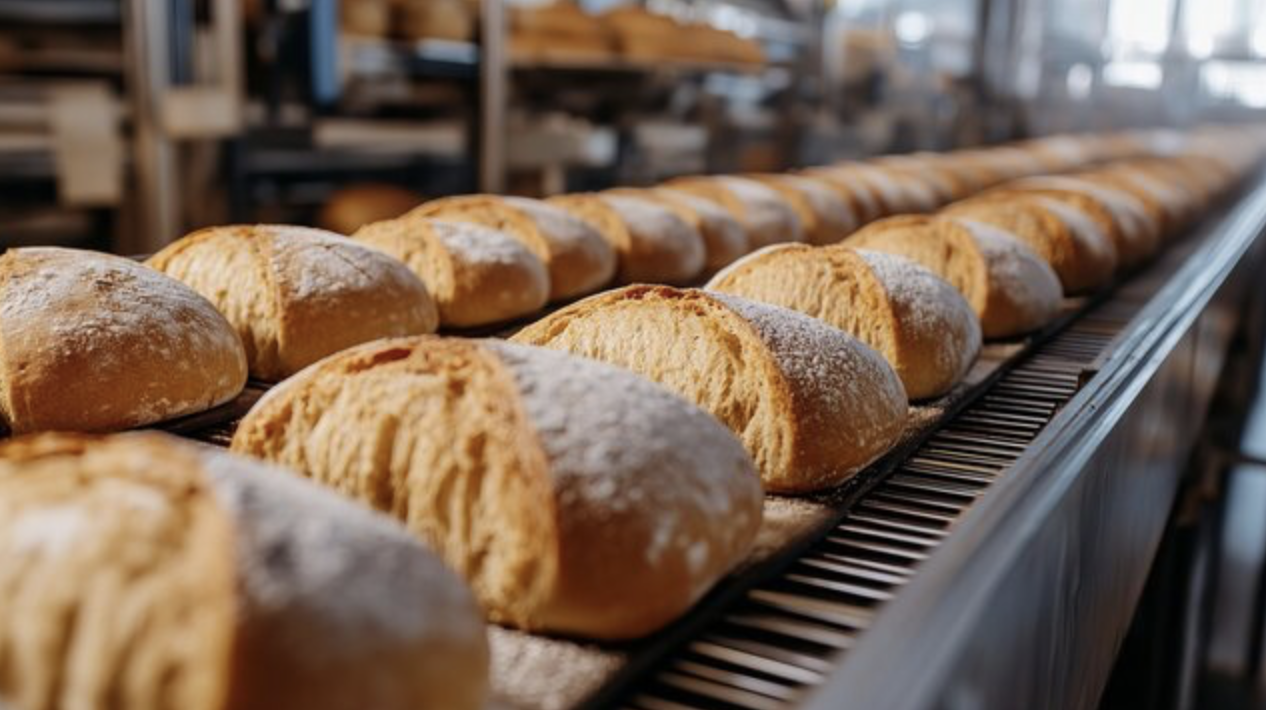
- /
- By Bolders
The food and beverage industry is one of the most highly regulated sectors, with quality and safety being top priorities. But even with the best efforts, recalls still happen—and when they do, they can have costly consequences. In 2022 alone, food recalls resulted in millions in losses and significant reputational damage. So, how can businesses better protect themselves? With a tool like SAP Integrated Business Planning (IBP), which is powerful and designed to anticipate risks and improve responsiveness before a recall crisis unfolds.
The Functional Problem: Lack of Visibility and Agility in Supply Chains
For many companies in the food and beverage space, the main challenge lies in the complexity of their supply chains. From sourcing raw materials to distributing final products, multiple steps are involved—any one of which could trigger a recall if something goes wrong.
But here’s the catch: many organizations are still relying on fragmented systems or spreadsheets that make it hard to track real-time data. This lack of visibility can delay responses to safety issues, causing slower recall actions and greater risks to consumers, not to mention potential regulatory fines.
The Solution: How SAP IBP Keeps You Ahead of Recalls
So, what can SAP IBP offer to food and beverage companies? SAP IBP connects every element of your supply chain with real-time, end-to-end visibility, enabling faster, more informed decisions. Here’s how it helps specifically with recalls:
- Predictive Analytics: SAP IBP uses advanced analytics to identify potential risks in the supply chain before they lead to product recalls.
- Real-Time Tracking: The platform allows you to monitor product flows, detect anomalies, and respond quickly when an issue arises.
- Collaborative Planning: Through synchronized planning with suppliers and partners, SAP IBP ensures that businesses are prepared for disruptions and can respond seamlessly to quality issues.
- Compliance Management: It also supports compliance with industry regulations, giving businesses the ability to meet safety standards and avoid penalties.
By implementing SAP IBP, food and beverage companies are not just reacting to recalls—they’re preventing them from happening in the first place.
Call to Action: Take Control of Your Supply Chain and Stay Ahead of Recalls
Being proactive about recall prevention is a competitive advantage in today’s market. With SAP IBP, your business gains the tools to enhance supply chain transparency, respond faster, and improve overall efficiency. Now is the time to explore how this solution can transform your approach to food safety and operational excellence.
Second Call to Action: Let’s Start a Conversation
Which challenge is your business currently facing? Share your thoughts and let’s discuss how SAP IBP can help your business thrive!
Do you have any questions about Bolders Consulting Group’s services? Or, are you looking for more information regarding our solution development services? Bolders Consulting Group’s team of world-class consultants are ready to answer any questions you may have.